Car
Frame Side View
This view of the
car frame shows the wing mount points at the top of the image, as well
as forward hull mounting points at bottom. The rearward mount will
eventually couple with aluminum angle attachments just above and
aft of the step. The engine will mount and hang off of the rear top
section of the car frame. The fuel tank goes in the center of the
structure. Spence did a good job of keeping the bulk of the
weight centralized and close to the center of lift. |
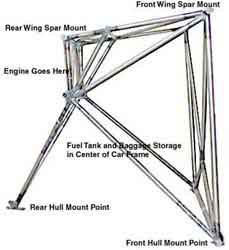 |